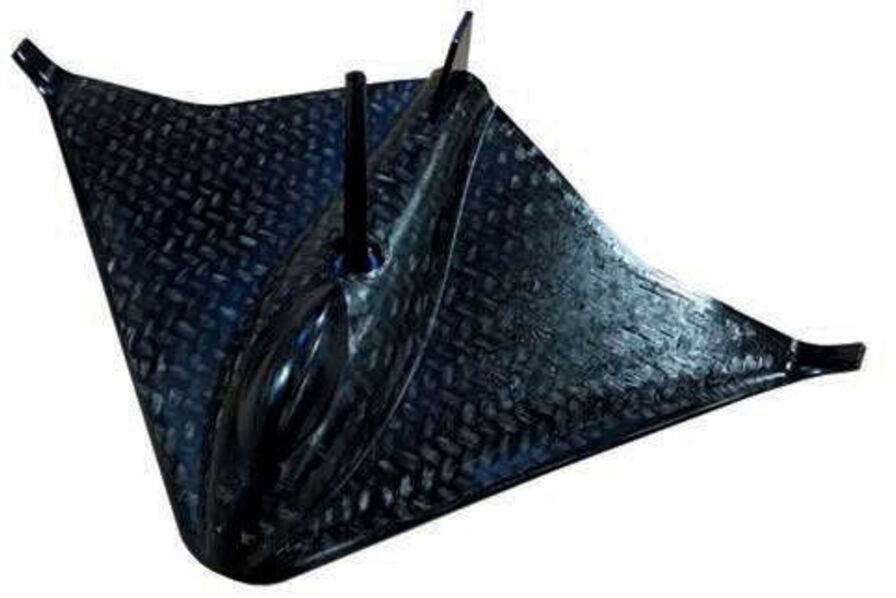
How to stamp a thermoplastic composite part with a drone geometry and overmold it around the perimeter in the same cycle without a post-molding finishing step? This is the request made by the IPC technical center to the mold maker Pernoud.
The company, which began working with thermoplastic composites in the 2010s, particularly through the collaborative Increase project, has indeed developed several key technological components to improve the productivity of processes such as thermocompression or stamping. The latest of these innovations is the retractable gripping.
Co-financed by the Auvergne Rhône-Alpes region, this innovation was developed as part of the Hyprod² platform of the IPC technical center. Its mission is to help manufacturers improve the competitiveness of their composites by acting on three complementary aspects: the development of lightweight, durable, and multifunctional composite parts; high-speed manufacturing processes that maintain the performance, reliability, and robustness of integrated functions; and the implementation of an eco-friendly approach through the wise choice of materials and technologies, and the end-of-life management.
The main challenge posed by IPC’s request was to maintain the organo-sheet during stamping so that it remains precisely positioned, without the holding system interfering during the overmolding surrounding the part.
The solution provided by Pernoud is a collaboration between a tooling and a gripping hand. The latter holds the organo-sheet precisely during its heating under infrared, then during its positioning in the tooling and its shaping. The organo-sheet is then progressively stamped according to the final shape, while the mechanical retraction of the gripping hand’s clamps can occur before the complete closure of the tooling, thus allowing the peripheral overmolding by clearing the functional areas.
This combination allows stamping and overmolding a part in the same cycle without compromising the overmolding and without needing post-molding finishing: it comes out of the press “Net-shape.” This design works on standard machines, whether vertical or horizontal. It reduces manufacturing costs and logistics associated with a thermoplastic composite part, also simplifying the integration of this technology for traditional plastic manufacturers.